The use of alternative fuels for aviation is increased due to concerns over fuel security, price stability and the sustainability of fuel sources. Concurrent reductions in particulate emissions from the alternative fuels are also expected because of changes in fuel composition including reduced sulfur and aromatic content. Aircraft are a unique anthropogenic source of pollution as they emit at both ground-level and high altitude. Ground-level emissions have an effect on local air quality in the regions surrounding airports, while emissions at altitude increase cloud cover and increase background levels of black carbon, which is estimated to be one of the strongest contributors to current global warming. Beside emissions from the lubrication oils, aircraft particulate emissions (including direct emissions of soot and secondary aerosols formed from the processing and partitioning of gas-phase emissions) are especially linked to the composition of the fuel. Aromatics in the fuel lead to the formation of soot, while fuel sulfur is converted to gas-phase sulfur dioxide (SO2) and then to particulate sulfate. Thus, changes to the composition of the fuel lead to changes in particulate emissions.
Above critical situation has created demand for alternative aviation fuel from non-petroleum fuel sources in commercial scale as “drop-in” fuels, allowing using in aircraft without engine modifications. Biomass can play a key role to provide the sustainable solution. It can produce a fuel with similar physical (such as viscosity and density) and combustion properties (such as heat of combustion, ignition delay, flame speed etc.) as petroleum – derived fuel but with distinct chemical compositions.
Process
The first step in the process is the production of syngas (a mixture of CO and H2) from the biomass feedstock. The syngas can be converted through the Fischer-Tropsch (FT) synthesis process to produce hydrocarbons and further processed to produce a fuel with a volatility range similar to conventional aviation fuel. This process leads to a fuel composed primarily of alkanes with very little aromatic content and no sulfur. These characteristic are beneficial when considering particulate emissions from aircraft engines burning FT fuels as low levels of aromatics resulting less soot, particularly at low engine power, low sulfur content leads to decreased formation of volatile aerosols.
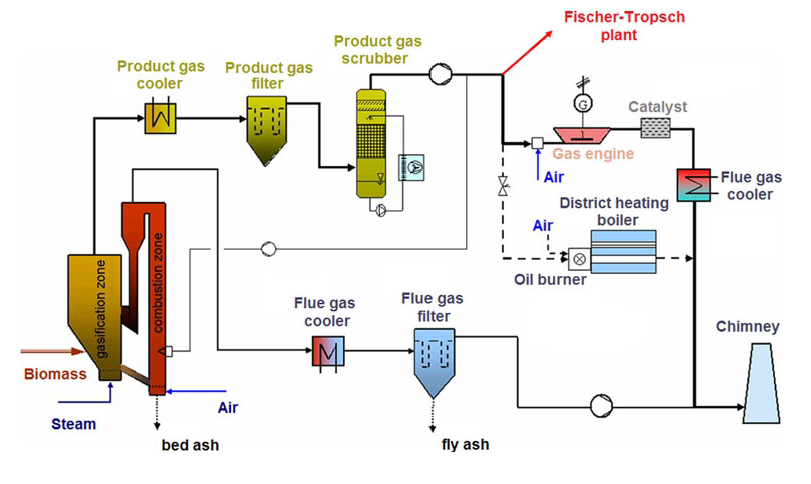
Biomass-to-Liquids technology consists of the production of long-chain hydrocarbons from syn gas by three main steps: biomass gasification in order to produce syn gas, FT synthesis and product upgrading by distillation and hydro-processing. FT synthesis offers the possibility of obtaining clean fuels and chemical feedstock. The basic chemistry of the synthesis consists in the hydrogenation of CO molecules from syn gas.
(2n+1) H2 + nCO | CnH2n+2 + nH2O | (1) |
2nH2 + nCO | CnH2n + nH2O | (2) |
2nH2 + nCO | CnH2n+2O + (n-1) H2O | (3) |
(2n-1) H2 + nCO | CnH2nO + (n-1) H2O | (4) |
CO + H2O | CO2 + H2 | (5) |
The main reactions are for alkanes and alkenes (Eqs. 1 and 2) synthesis. Methanation and water- gas shift reaction (Eq. 5) are undesirable due to consumption, when H2/ CO ratio is almost 2. In case the synthesis gas has a low concentration of H2, the water- gas shift reaction becomes necessary in order to increase the H2/ CO ratio. Alcohols (Eq. 3), aldehydes and ketones (Eq. 4) are also produced in the FT synthesis. Cobalt and iron based Catalysts are used to activate the FT reactions.
Syngas from DFB gasification plant is introduced to the FT synthesis plant, which consists of the following steps :-
- RME scrubber for additional drying and cleaning of the syngas from the rest of the tars, particles, NH3 and aromatics like naphthalene and BTX.
- Activated charcoals for adsorbing and cleaning the gas from the BTX and sulfur compounds.
- Compression in two steps by diaphragm pumps and a piston compressor up to 25 bar.
- Finally, gas cleaning on fixed bed reactors of ZnO and CuO adsorbers. ZnO is used for precisely removing H2S, mercaptans and two CuO adsorbers remove the residues of the thiophene and chlorine compounds.
- Slurry FT reactor.
- High – pressure fluid separator.
- Off-gas condenser to collect all possible light products.
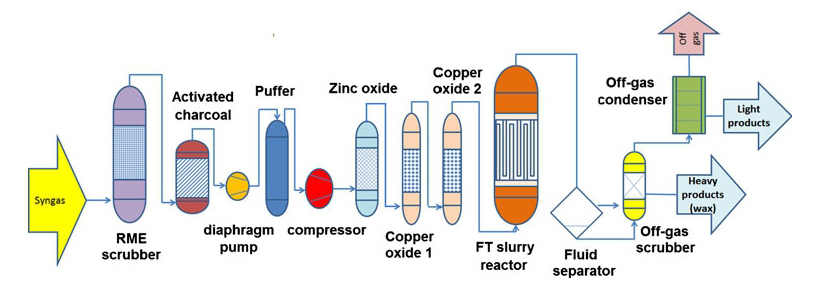
The potential use of FT fuels as aviation fuel is essential for reduction of the dependence on fossil oil and for development of low-carbon sustainable fuel sources.